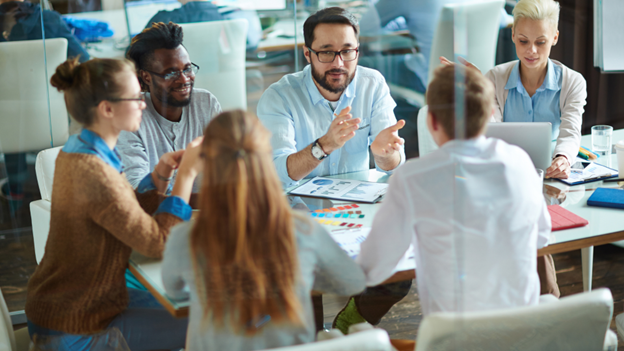
03 Jul Cross-Training Employees To Support Scheduled Maintenance Efforts
Many organizations still depend heavily on a few specialized technicians to keep equipment operating. While this approach often feels efficient in the short term, it can lead to hidden vulnerabilities that disrupt business. If a key team member calls in sick or moves on, the maintenance backlog grows quickly, delaying production and driving up costs.
Unexpected absences can leave operations exposed to preventable downtime and reactive fixes that drain budgets. By cross-training employees, companies distribute critical knowledge and build a more resilient workforce that can step in confidently. With the right training and clear boundaries, teams can manage routine maintenance tasks consistently and keep essential equipment in top condition. Cross-training not only reduces risk but also creates an environment where employees feel invested and valued for their diverse contributions.
Designing an Effective Cross-Training Program
Building a successful cross-training program requires a thoughtful approach that aligns with your facility’s goals. It starts by documenting scheduled maintenance workflows to see where routine tasks can be shared without disrupting more advanced work.
Managers should look for employees who show interest and an aptitude for learning hands-on procedures. Training materials should be clear and visual, making it easy for team members to follow each step independently. Supervised practice reinforces lessons and gives employees a chance to build confidence under the guidance of experienced technicians.
Periodic assessments ensure everyone meets the expected standards before they perform tasks on their own. Maintaining detailed records of training progress allows managers to track development and address any gaps quickly. Over time, this structured approach builds skills systematically and ensures consistency across the maintenance team.
Why Relying Solely on Specialized Maintenance Staff Can Backfire
Relying only on a handful of experts may seem practical, but it limits flexibility and raises the stakes whenever something unexpected happens. When maintenance demands surge or a technician becomes unavailable, delays become unavoidable. Production schedules start to slip, and teams must scramble to find qualified support.
Over time, this dependence can frustrate employees and contribute to burnout, as specialists feel constantly under pressure to respond to every problem. In many facilities, this dynamic drives costs higher because reactive repairs are almost always more expensive than planned maintenance.
Cross-training employees offers a proactive solution by spreading knowledge across the workforce. When more people understand how to handle basic preventive tasks, maintenance becomes predictable and consistent, even if staffing changes. Organizations can maintain equipment uptime and avoid bottlenecks without sacrificing safety or quality.
How Cross-Training for Maintenance Increases Flexibility and Reduces Downtime
Cross-training empowers employees to step in confidently when maintenance needs arise, especially during times of high demand or unexpected absences. Instead of waiting for a specialist, cross-trained team members can complete essential preventive tasks and keep operations moving.
This approach makes scheduling easier because managers have more options to fill gaps without delaying work orders. Employees who learn new skills often feel more engaged, knowing their efforts help protect equipment and prevent costly downtime. Over time, these shared responsibilities build a culture of accountability that reinforces collaboration.
When technicians see coworkers capable of handling routine inspections, filter changes, or basic troubleshooting, they can focus on complex repairs that truly require their expertise. This balance keeps workloads manageable and ensures equipment receives timely care, ultimately strengthening reliability and performance.
Identifying the Right Skills to Cross-Train
Not every maintenance task should be delegated, so it’s important to identify which activities fit safely within a cross-training program. Simple procedures like basic lubrication, cleaning filters, or resetting alarms can be taught effectively without compromising safety.
Visual inspections also work well because they help detect early signs of wear before they become serious problems. When deciding what skills to include, managers should consider both the complexity of the task and the level of risk involved. Advanced repairs or highly technical adjustments still belong in the hands of trained specialists.
Clear guidelines help employees understand where their responsibilities begin and end, reducing confusion or overreach. By defining these boundaries from the start, organizations create a structured framework that supports consistent results and avoids any compromise in maintenance standards.
Motivating Employees to Participate in Cross-Training
Even the best-designed program will struggle if employees don’t feel motivated to engage. One way to inspire participation is to show how cross-training leads to career development and more job security.
Employees who broaden their skills often find new opportunities to advance within the organization. Recognizing achievements publicly and offering small incentives can also help reinforce the value of learning. Managers should communicate how cross-training supports everyone, reducing stress when workloads increase or staffing changes occur.
When employees understand that learning new tasks protects the team from disruption, they feel more invested in the outcome. Sharing stories of colleagues who have benefited from cross-training helps make the benefits feel real and attainable. Over time, this positive reinforcement builds enthusiasm and trust among employees, making employees eager to take part in the process.
Ensuring Consistency and Quality Across Teams
Maintaining high standards is essential when responsibilities expand beyond a small group of specialists. Consistency begins with clear procedures that outline exactly how each task should be completed.
Senior technicians play a crucial role by supervising early practice sessions and verifying that work meets expectations. Regular reviews and constructive feedback help employees fine-tune their skills and stay aligned with safety requirements. Rather than micromanaging every step, managers can focus on reinforcing good habits and addressing occasional mistakes before they become patterns.
Documentation also supports accountability, providing a record of completed tasks and any issues that needed correction. This transparency not only improves performance but also builds confidence across the team. With clear guidance and consistent oversight, cross-training becomes a reliable strategy that strengthens both capability and trust.
Measuring the Impact on Maintenance Performance and Efficiency
Tracking results is the only way to know whether cross-training investments pay off. Metrics like the time it takes to complete preventive tasks, the number of overdue work orders, and the frequency of emergency contractor use reveal how training affects performance.
Facilities that embrace cross-training often see faster response times and fewer delays when unplanned absences occur. Reduced reliance on outside contractors helps control costs and keeps maintenance spending predictable. Employee surveys can also provide valuable insight into engagement and satisfaction, as learning new skills tends to improve morale and reduce turnover. By collecting data regularly, managers can pinpoint areas for improvement and celebrate progress. Over time, these metrics show that cross-training does more than fill skill gaps—it builds a stronger, more resilient operation that benefits everyone.
Building a Resilient Maintenance Culture
Cross-training employees is not just a temporary fix for staffing shortages. It’s a strategic investment that transforms maintenance into a proactive, collaborative effort. By spreading essential knowledge across your team, you strengthen your operation’s ability to respond to challenges and protect equipment performance.
Employees who develop new skills feel more confident and valued, which improves engagement and retention. Clear procedures, consistent oversight, and thoughtful recognition create a foundation where shared responsibilities thrive. Over time, cross-training reduces downtime, controls costs, and builds trust among colleagues. As your organization grows, a well-trained, adaptable team will be ready to handle whatever comes next, making cross-training one of the most effective tools for long-term success.
Frequently Asked Questions
How long does it take to cross-train employees for basic maintenance tasks?
Most employees can become proficient in simple maintenance activities within four to eight weeks, depending on their prior experience and the complexity of your equipment.
Will cross-training employees compromise the quality of maintenance work?
No. When you combine clear procedures, structured practice, and oversight by experienced technicians, cross-training improves consistency without lowering standards.
What is the best way to track training progress and performance?
Many companies use CMMS platforms or digital training logs to document skills, monitor certifications, and verify that employees meet competency requirements before taking on new responsibilities.
About The Author
Daniel Martin loves building winning content teams. Over the past few years, he has built high-performance teams that have produced engaging content enjoyed by millions of users. After working in the Aviation industry for ten years, today, Dani applies his international team-building experience at organiclinkbuilders.com to solving his client’s problems. Dani also enjoys photography and playing the carrom board.
No Comments